Wasafishaji wa ultrasonicni mashine muhimu katika kusafisha viwanda na maabara, inayojulikana kwa ufanisi wao wa juu na uwezo wa kusafisha haraka. Licha ya faida zao, watumiaji wengi wameripoti kuwa mashine hizi huwa "tete" kwa wakati, mara nyingi hupata hitilafu au hata kuharibika. Hii inasababisha kupungua kwa tija, kuongezeka kwa gharama za ukarabati, na wakati mwingine kuathiri utendaji wa kusafisha. Kuelewa sababu kuu za uvaaji safi wa ultrasonic ni muhimu kwa kupanua maisha ya vifaa hivi na kupunguza viwango vya kushindwa.
Mambo Muhimu Yanayochangia Uvaaji wa Kisafishaji wa Ultrasonic
An kusafisha sehemu za ultrasoniclina vipengele kadhaa muhimu, ikiwa ni pamoja na transducer, tank kusafisha, mfumo wa umeme, na kudhibiti moduli. Vipengele hivi vinakabiliwa na aina mbalimbali za matatizo katika mazingira ya juu-frequency, yenye nguvu ya juu, na kusababisha kuvaa na uharibifu unaowezekana. Chini, tunachunguza sababu za kawaida za kuvaa na kushindwa katika wasafishaji wa ultrasonic.
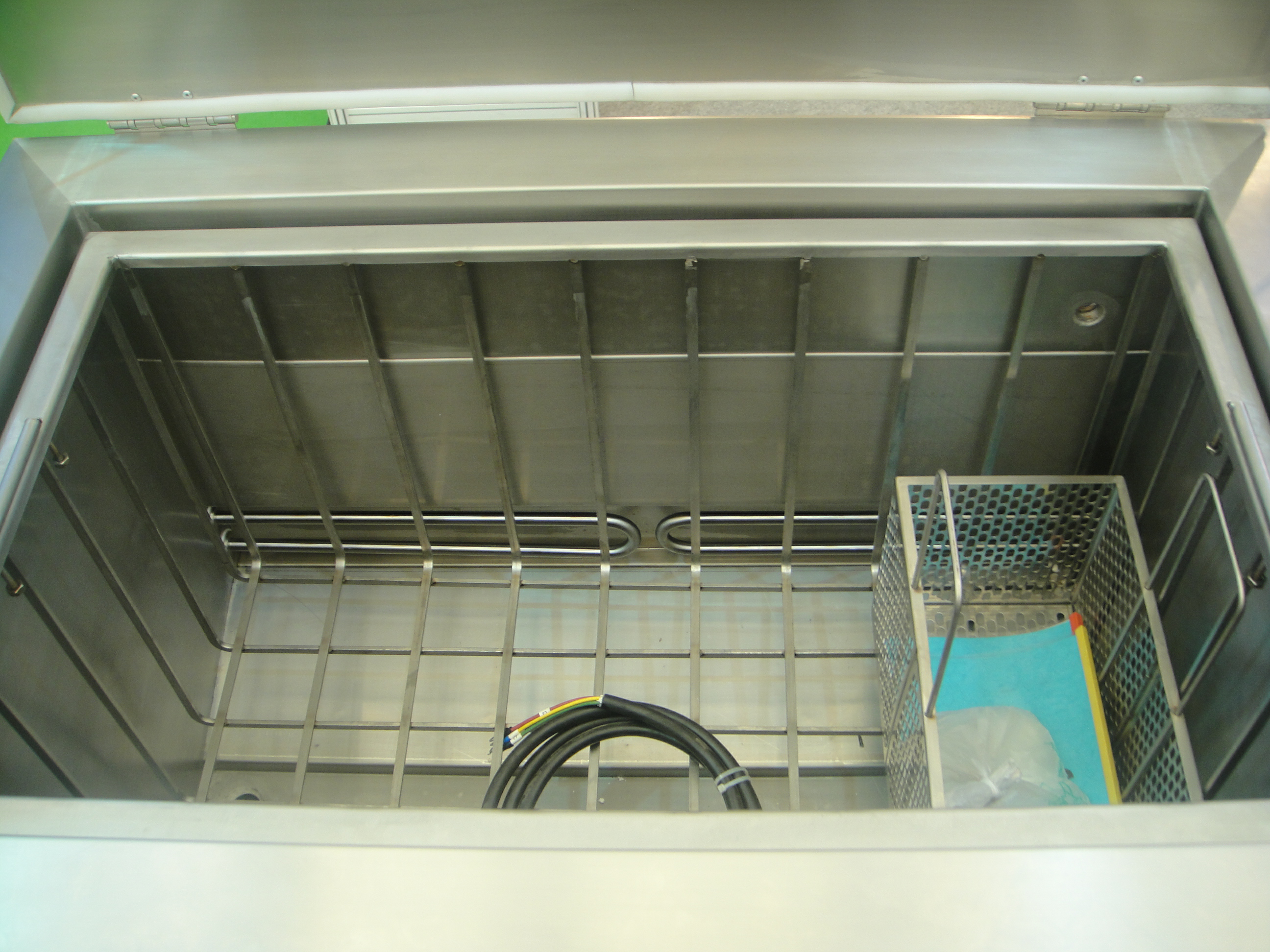
1. Kushindwa kwa Transducer
Transducer ina jukumu muhimu katika kusafisha ultrasonic kwa kubadilisha nishati ya umeme kuwa mitetemo ya mitambo, kutoa mawimbi ya ultrasound. Hata hivyo, kutokana na uendeshaji wa muda mrefu wa juu-frequency na high-nguvu, transducers ni hasa kukabiliwa na kushindwa.
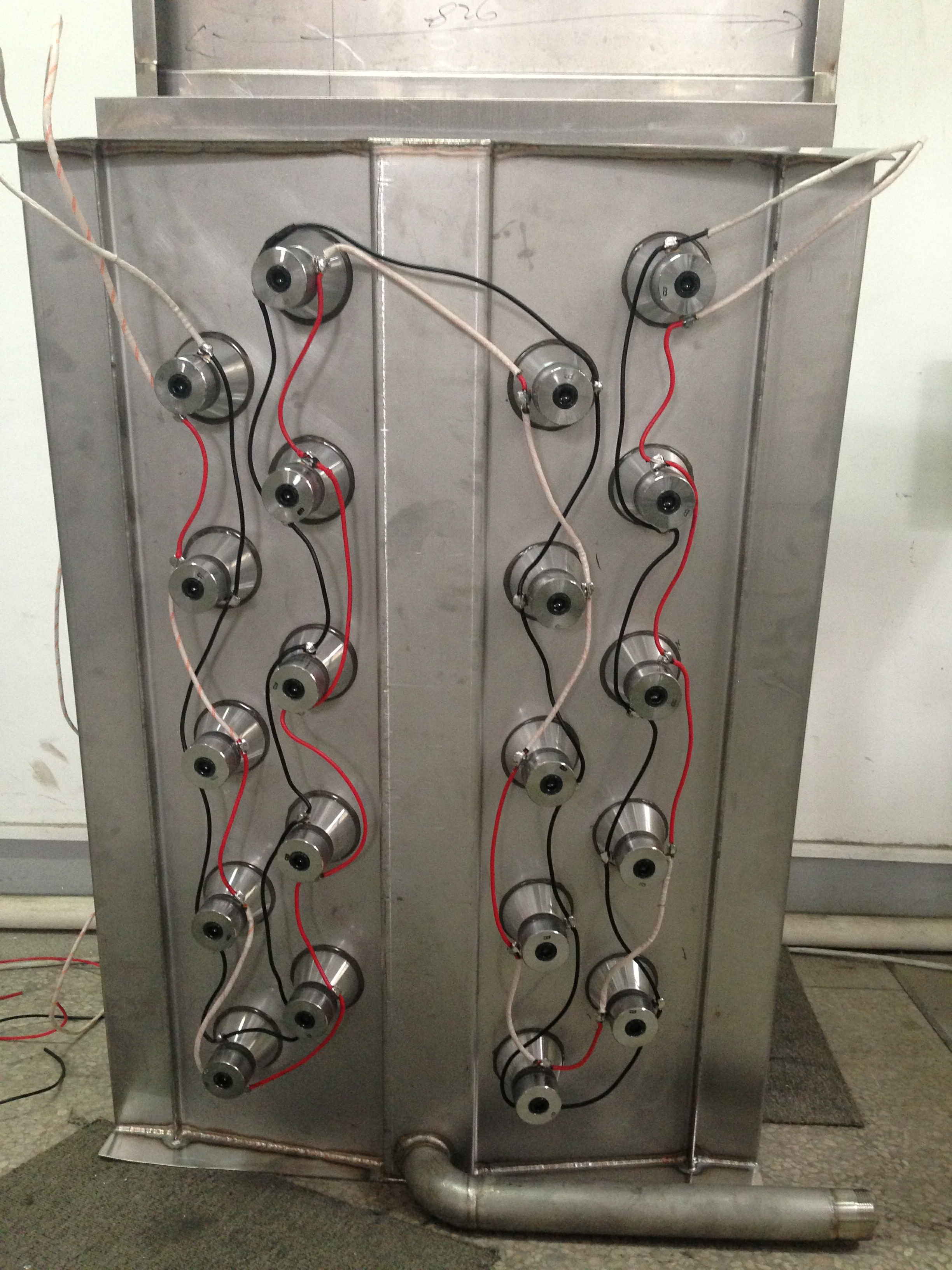
Kuzidisha joto:Transducer huzalisha joto kubwa wakati wa operesheni, na bila utaratibu wa baridi wa ufanisi, joto la juu linaweza kuharibu nyenzo za piezoelectric za transducer, na kusababisha nyufa au hata delamination.
Mizunguko ya Mara kwa Mara ya Kuanza-Kuacha:Kila wakati mashine inapowashwa au kuzimwa, transducer hupitia mabadiliko ya haraka ya mtetemo. Mzunguko unaorudiwa wa aina hii kwa muda unaweza kusababisha uchovu wa ndani, na kufanya sehemu hiyo kuwa hatarini zaidi kwa uharibifu.
Uharibifu wa Kimwili:Mishtuko ya nje au mitetemo ya kimitambo inaweza kuhatarisha muundo wa ndani wa transducer, kuathiri uthabiti wake na kusababisha matokeo yasiyolingana ya ultrasonic.
2. Kuvaa na Kuharibika kwa Tangi ya Kusafisha
Ingawa matangi ya kusafisha kwa kawaida hutengenezwa kwa nyenzo kama vile chuma cha pua ambayo hustahimili kutu, bado yanakabiliwa na uchakavu kutokana na mfiduo wa muda mrefu hadi mitetemo ya masafa ya juu na mawakala wa kusafisha kemikali.
Mmomonyoko wa Cavitation: Cavitation, mchakato ambapo Bubbles vidogo huingia ndani ya kioevu, ni muhimu kwa mchakato wa kusafisha ultrasonic. Ingawa ni bora katika kuondoa uchafu, cavitation pia huathiri nyuso za ndani za tank ya kusafisha, na kusababisha microcracks au mashimo kwa muda, ambayo inaweza hatimaye kusababisha tank kushindwa.
Kutu ya Kemikali: Kazi nyingi za kusafisha viwanda zinahitaji matumizi ya ufumbuzi wa kusafisha tindikali au alkali. Suluhisho hizi, zinapojumuishwa na vibrations za ultrasonic, zinaweza kuharakisha kutu ya tank ya kusafisha. Ingawa chuma cha pua ni sugu kwa kiasi fulani, mfiduo wa muda mrefu kwa kemikali kali bado unaweza kusababisha uoksidishaji au uharibifu wa nyenzo.
3. Kushindwa kwa Mfumo wa Umeme
Mfumo wa umeme wa akisafishaji cha ultrasonic cha baraza la mawazirini ngumu, inawajibika kwa kudhibiti pato la nguvu, frequency, na vigezo vingine. Kushindwa ndani ya mfumo wa umeme ni chanzo kikubwa cha malfunction ya vifaa.
Upakiaji kupita kiasi: Nguvu ya pato la mashine ikizidi uwezo wa muundo wa mfumo, mfumo wa umeme unaweza kuzidiwa, na kusababisha bodi za saketi au vipengee vingine vya kielektroniki kuteketea.
Frequency Mismatch: Frequency ya kisafisha ultrasonic inadhibitiwa na saketi za oscillation kwenye ubao wa mzunguko. Iwapo saketi hizi hazifanyi kazi vizuri au kuwa na usawa, inaweza kuzuia transducer kutoa masafa thabiti, ambayo huathiri ufanisi wa kusafisha.
Vipengele vya Kuzeeka: Baada ya muda, sehemu za kielektroniki za mfumo huharibika, hasa chini ya hali ya joto la juu endelevu. Uharibifu huu hupunguza utendaji wa insulation, ambayo inaweza kusababisha mzunguko mfupi au kushindwa kwa vipengele.
4. Matumizi Yasiyofaa
Kando na ulemavu wa vifaa, operesheni isiyofaa ni sababu kuu ya uchakavu wa visafishaji vya ultrasonic. Matumizi yasiyo sahihi hayawezi tu kupunguza ufanisi wa kusafisha, lakini pia kuongeza hatari ya uharibifu wa vifaa.
Viwango vya Chini vya Kioevu: Ikiwa kioevu kwenye tanki la kusafisha ni kidogo sana, mitetemo ya kibadilishaji sauti huenda isikatizwe ipasavyo, na kuifanya ifanye kazi chini ya mkazo na uwezekano wa kusababisha uharibifu.
Suluhisho Zisizofaa za Kusafisha: Kutumia visafishaji vyenye asidi nyingi au alkali, au visivyooani na vifaa vya kisafishaji, kunaweza kuharakisha ulikaji wa ndani, kuongeza uchakavu na kupunguza muda wa jumla wa maisha wa kifaa.
Uendeshaji wa Nguvu ya Juu Kupita Kiasi: Kuendesha kisafisha ultrasonic kwa nguvu kamili kwa muda mrefu kunaweza kuongeza kasi ya kuvaa kwa transducer na tank ya kusafisha, na kusababisha kuzeeka mapema kwa vifaa na kuongeza gharama za matengenezo.
Mbinu za Kuongeza Muda wa Maisha ya Visafishaji vya Ultrasonic
Ingawa visafishaji vya ultrasonic hupata uvaaji wa asili, kuchukua hatua zifuatazo za kuzuia kunaweza kupanua maisha yao ya kufanya kazi.
1. Ukaguzi na Matengenezo ya Mara kwa Mara
Angalia Transducers:Mara kwa mara kagua vibadilishaji joto kwa joto kupita kiasi, nyufa au mitetemo isiyo ya kawaida. Badilisha au urekebishe mara moja vibadilishaji sauti vyenye kasoro ili kudumisha utendakazi bora.
Kagua Tangi la Kusafisha:Kuchunguza mara kwa mara tank ya kusafisha kwa ishara za kutu, nyufa, au mashimo. Tumia mawakala wa kusafisha kwa upole na epuka kemikali kali ili kuzuia uharibifu usio wa lazima.
Ukaguzi wa Mfumo wa Umeme:Hakikisha kuwa nyaya za umeme, plagi na saketi za ndani ziko katika hali nzuri. Fanya ukaguzi wa mara kwa mara kwenye pato la nguvu na mzunguko, na uepuke kupakia kifaa kupita kiasi, haswa wakati wa operesheni ya nguvu ya juu.
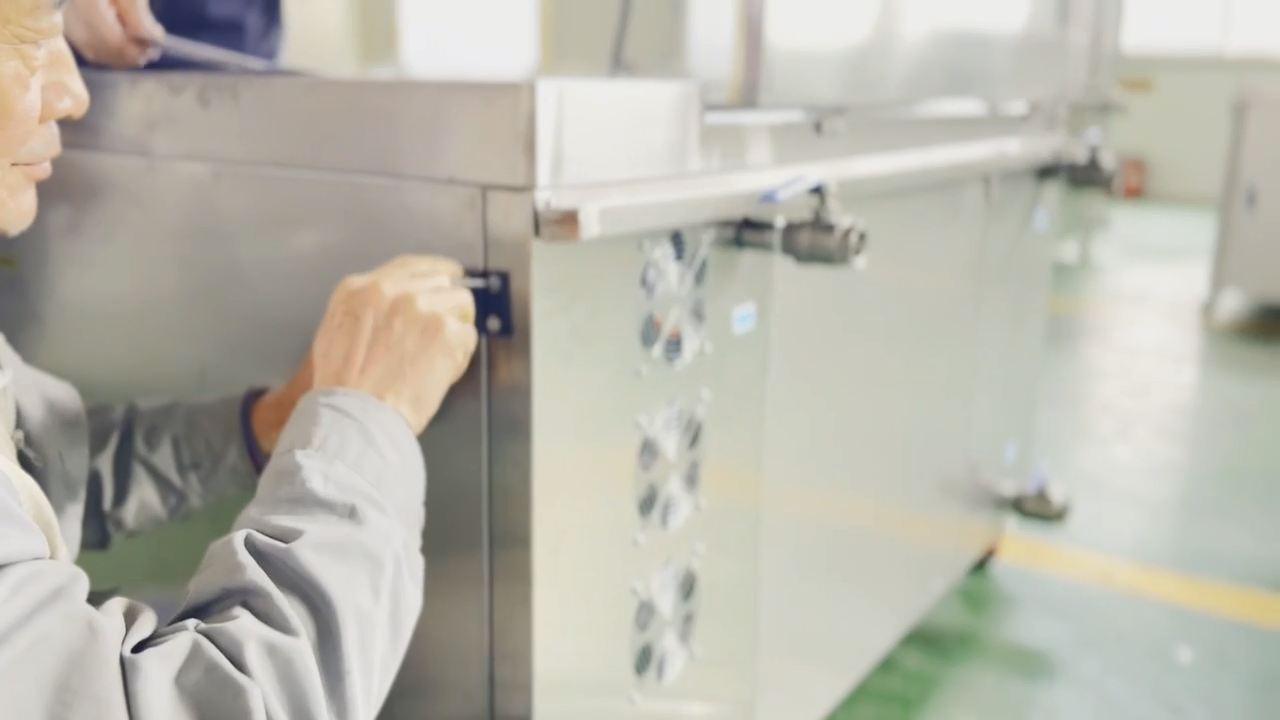
2. Dhibiti Mazingira ya Uendeshaji
Hakikisha uingizaji hewa wa kutosha:Weka mazingira ya kazi yenye uingizaji hewa mzuri ili kuzuia overheating ya transducer na mfumo wa umeme. Kusakinisha vifaa vya ziada vya kupoeza kunaweza kusaidia kupunguza halijoto na kuboresha maisha marefu ya kifaa.
Zuia Uharibifu wa Kimwili:Epuka kuweka vifaa katika maeneo ambayo yanaweza kukabiliwa na mshtuko wa nje au mitetemo ili kulinda transducer na tank kutokana na uharibifu.
3. Matumizi Sahihi ya Kifaa
Rekebisha Nguvu na Muda wa Matumizi:Epuka operesheni ya muda mrefu ya nguvu ya juu. Rekebisha mipangilio ya nishati kulingana na mahitaji ya kusafisha, na uzingatie kutumia mashine mara kwa mara kwa kazi ndefu za kusafisha ili kupunguza uchakavu wa kibadilishaji umeme.
Tumia Suluhisho Zinazofaa za Kusafisha:Chagua mawakala wa kusafisha ambayo yanaendana na nyenzo za mashine. Hakikisha kuwa kiwango cha kioevu cha kusafisha kiko ndani ya safu inayopendekezwa ili kuzuia kukimbia kukauka, ambayo inaweza kuharibu transducer.
4. Kutunza Kumbukumbu za Kina
Weka rekodi za kina za shughuli zote za matengenezo, ikijumuisha ukaguzi, ukarabati na uingizwaji. Hati hizi husaidia kufuatilia hali ya mashine na huwaruhusu watumiaji kutambua matatizo yanayoweza kutokea mapema.
Hitimisho
Uchakavu wa kisafishaji cha ultrasonic unaweza kuhusishwa na sababu kadhaa, ikiwa ni pamoja na kushindwa kwa transducer, uharibifu wa tanki, hitilafu za mfumo wa umeme na matumizi yasiyofaa. Ingawa kiwango fulani cha uvaaji hakiepukiki, utunzaji unaofaa na matengenezo ya mara kwa mara yanaweza kupanua maisha ya vifaa hivi. Kwa watumiaji wa mara kwa mara, kudumisha vifaa katika hali bora sio tu kunaongeza ufanisi wa kusafisha lakini pia hupunguza gharama za kupunguzwa na ukarabati.
Muda wa kutuma: Feb-11-2025